Ask the Drying Expert – Your Questions Answered
Resin Drying Expert Mark Haynie answers your technical questions for troubleshooting your plastic resin drying. Submit your own question in the box to the right.
What determines resin moisture adsorption rate and capacity?
The moisture adsorption rate and capacity of resin are determined by several factors. These include the type of resin, the environmental conditions, the degree of crystallinity, and the presence of fillers or additives.
For example, hygroscopic resins have a higher affinity for water molecules and tend to absorb moisture more readily than non-hygroscopic resins. Environmental conditions such as temperature and relative humidity can also influence moisture absorption rates. Higher temperatures and higher relative humidity levels generally result in faster moisture absorption. The degree of crystallinity of the resin can also affect its moisture adsorption rate and capacity. Resins with higher degrees of crystallinity tend to have lower moisture adsorption rates and capacities. Finally, the presence of fillers or additives in the resin can also affect its moisture adsorption rate and capacity. Certain fillers or additives can act as moisture barriers and reduce the resin’s ability to absorb moisture.
What is the best dryer for PET regrind drying for running preforms?
If you’re looking for the best type of dryer to use for PET regrind drying when running preforms, it depends on a few factors. First, you’ll want to consider the source of the regrind and how it’s being combined before it goes into the Injection Machine.
Luckily, dryers have come a long way in terms of energy efficiency and user-friendliness. Both dual bed and wheel dryers can work well, but wheel dryers tend to have a more consistent dew point and temperature, which is especially important for preform manufacturing. (The machines, often Husky brand, require a consistent temperature to the machine throat for the best preform production.)
One option you might consider is Novatec’s IntelliPET dryer, which is specifically designed for preform production and consistency. It also features variable frequency drives that adjust power based on the material rate, resulting in lower energy usage compared to older models.
If the regrind is preform regrind, you can generally add it in up to 10-15% without much hardware change. If the regrind is re-pelletized, you can use it much like virgin resin, although it may have a slightly lower IV than virgin resin.
However, if the regrind is PCR (post-consumer) flake, there are some additional factors to consider. PCR has already been through a heat cycle and has a lower IV, as well as a tendency to produce volatile compounds that can contaminate the desiccant materials during the drying process. To prevent this, you may need to add an additional treatment step to the hopper’s return air to limit and desiccant contamination.
What are some potential issues that could cause hard shell luggage cases (70% resin, 30% regrind) to break during drop tests?
One of our experienced PC processors suggested a few potential issues that may be causing the shells to break after drops:
- The resin may not be properly dried, and since the PC is colored, you may not see the air bubbles, and thermoforming usually doesn’t show the kind of surface splay you would see with injection molding. Sheet is thermoformed too hot.
- The regrind quality may be poor, as it could be a 2nd, 3rd, 4th generation of regrind and the PC has somewhat degraded from the multiple heat histories.
- There may be a contaminant in the regrind that becomes a weak point compared to the PC resin.
- Improperly drilled holes for hinges or saw cutting during trimming could cause weak spots or micro-cracks.
- Cleaning agents used after processing may not be compatible and cause micro-stress cracking.
- It would be helpful to see a photo of a broken shell to determine if the cracks are brittle (like what one would see with say polystyrene) or ductile tears.
- The drop test may also be too severe.
If you’d like to send us photos, we can have our expert take a look and provide further insights. We’re here to help you find a solution!
How often should desiccant be changed out, assuming we run 24/7?
I have seen desiccant running well in service for over 10 years but the supplier guideline is 3-5 years. Desiccant normally fails due to poor filter maintenance or, in cases of high levels of volatiles, off-gassing from material. The best way to preserve desiccant is to change filters on a regular basis and always turn the dryer off when changing filters. There is no reason to change desiccant that is providing good dew point and airflow performance.
How do we minimize the amount of dust entering the dryer either through resin or regrind?
My first recommendation is to install a good cyclone. Second make sure that your filter maintenance is good and that your filter changing procedure prevents dust from getting past the filter housing. It’s also possible to reduce dust by installing several outlets in the top of the hopper. Multiple outlets balance the airflow in the hopper and helps reduce the velocity at each outlet. You can also weld a drop tube around the loader throat which contains the material causing it to flow slowly into the hopper at a steady state.
What material would you use to insulate a 4,500 lb Hopper?
Most companies use standard fiberglass insulation which has proven to have the best cost benefit ratio. There are many other materials available but they are much more expensive and perform marginally better. The goal is to limit the external skin temperature to a point where it is warm to the touch but will not burn you. Also, don’t limit this to just the hopper. Some of the biggest savings we’ve seen is in proper insulation of the heater boxes and piping and hopper cones.
If a single blower supplies multiple hoppers, is there any opportunity for improving airflow control? Each hopper has independent return air.
Yes, it can be done but it is probably too expensive for the return on investment. You can put individual dampers on the inlet of each hopper to control airflow. If you add airflow sensors, you will start spending more money but achieve better control.
How can a single central dryer, dry several different materials?
A Central Dryer produces -40˚ dew point process air but has no process heater. The dry air is piped to multiple drying hoppers, each having its own heater/blower. These hoppers can contain different resins in different colors. The heater/blower on each hopper is adjusted to match the drying temperature of the material in that hopper.
The throughput of the central dryer is matched to the number of drying hoppers being served. A central drying system may consist of more than one central dryer, each serving multiple dryers.
A central material conveying system typically feeds material to the drying hoppers and then, on to processing machines.
A Quick Selection Manifold can be used to shuttle materials from any given material source to any given hopper so material changes occur at the drying hopper, reducing the time required for changeover.
Central Drying Systems reduce energy costs, labor costs, material losses and safety issues.
Can a dual bed desiccant dryer be retrofitted with a desiccant wheel?
The use of a desiccant wheel requires a new dryer. If you have a dryer that works well now, it may be best to continue to use it and look at things like water flow control, cycle timing and insulation to improve the energy of the system. However, when you look at a dryer replacement or a new line, the opportunity becomes very attractive.
We have a desiccant wheel dryer with no dew point monitor. Running a PET dryer at 320°F, should this give us dry material? We dry the material for 4.5 hours.
It’s not just time and temperature but also air flow rate and hopper design that needs to be considered. If the air flow is correct and the hopper is well designed to provide uniform air and material flow, PET processing usually does well with 4-6 hours at 320-350° F.
We pre-dry all our materials in a separate area out back and seem to have different molding problems throughout the year. Sometimes things run perfect for long periods of time, and then for no apparent reason, we start getting streaks, bubbles and other problems. What gives?
There are several possible reasons for the problems you are having. It could be that the problems are related to the condition of your incoming material. In colder and dryer times of the year, when the air outside is dry, the material is already fairly dry. But, when the weather is humid, the material is more humid and your dryer must work harder to remove its accumulated moisture. An older, or outmoded dryer will have a more difficult time providing uniform drying results. Check how old your desiccant is and replace it if it is more than 2 years old. Make sure all heaters are operating at full capacity and, of course, the blowers of your dryer must be operating correctly. Make sure the process and regeneration filters are clean because dirty filters can reduce the airflow, which has a direct effect on the efficiency of the dryer.
Jeff Rodway, Service Manager, Novatec Inc.
How negative must we be on the hoppers to pull air through the hopper back to the dryer? At present, we are pulling atmospheric air into the drying hopper.
Typically, drying hoppers operate at a positive pressure on the inlet and at a very slight vacuum to near neutral at the outlet. By restricting the inlet enough that the hopper operates at a vacuum, you may be limiting the drying air to the point that good drying may not occur and atmospheric air enters the hopper even adversely affecting drying further.
Additionally, the vacuum in the hopper can lead to difficulties in the hopper discharging properly into the convey lines and limit the available capacity if the convey pumps.
Is the dryer connected to more than one hopper? If so, I recommend that the primary restriction occurs at the hopper outlet rather than the inlet.
Currently using PVC durometer 65 bubbles in the injected outsole.
Although PVC is typically not hydroscopic, the presence of moisture on the surface can lead to inconsistent processing and the requirement for adjustments in the Injection Molding Machine.
The use of a Hot Air Dryer will remove the surface moisture and keep the PVC at a consistent temperature such that machine process parameters do not require as much monitoring and result in a more consistent product.
There are also IMM parameters that can lead to bubbles in the PVC. Please contact your machine vendor for suggestions that they may have.
How does high return air temperature experienced running PET affect the desiccant’s ability to adsorb more moisture?
The optimum performance of a desiccant occurs at near-ambient temperatures. Temperatures in excess of this lower the desiccant capacity and require that the air be cooled before going to the desiccant. This cooling of the air, for better adsorption, means that you have heated the air unnecessarily and thrown that heat into cooling water which requires more process heat to be re-added.
Novatec’s Power Guard systems continuously monitor the return air temperature and adjust the process airflow for optimum drying and minimum energy usage through a patented process that also adjusts the set point based on resin temperature.
I have heard that Cactus dryers do not work well unless there is only surface moisture because they use ambient air passed over heaters. Is this correct?
The Cactus is typical of hot air dryers with the exception that it uses compressed air instead of blower power to move the air. Because of this, it will be slightly lower in dew point, at times, if your compressed air is very dry. However, it will not be more consistent than your plant relative humidity. This can be an issue, especially in the summer.
When drying PU, it is usually important to control both the temperature and resin moisture to get consistent product flexibility and strength.
There are other dryers that use compressed air and a membrane and develop very consistent processing of PU. The NovaDrier is a good example of these and it uses far less power and compressed air than any other of its kind. The dew point and temperature are consistent, year round.
Why is my polycarbonate (PC) not drying completely? I’m following the instruction manual, and everything seems to be working correctly. I’m using a compressed air dryer and I was told that it would dry most materials under most conditions.
We’ve heard this story before. Unfortunately, you never know when the problem will crop up. Compressed air dryers only produce a dew point of about -10 degrees, under the best of circumstances, but summer temperatures or high humidity can push the dew point up to +10 or +20 degrees. That’s when you notice defects in your molded products.
There are also other problems with regular compressed air dryers but let’s concentrate on your current problem.
First, I think you should call the manufacturer of your dryer and see if there is any way to return it, depending on how old it is and what your warranty says. If that is not possible, ask if they have a membrane option. If you buy the membrane option and install it, you will get -40˚dew point process air and that should solve the current problem.
Note that regular compressed air dryers consume a lot of compressed air and when you add an optional membrane, the compressed air usage goes even higher. Next time you buy a dryer, consider one with a built-in membrane to save lots of energy and be guaranteed that you can dry all resins, regardless of the time of year.
How do I know whether resin dryer desiccant beads are still good?
- Visual inspection – Color should be creamy, eggshell white in color. If it is brown or black, replace the desiccant..
- Crush test – Take a few pellets and put between your fingertips. If you can crush the pellets, replace the desiccant
- Water test – After the desiccant has been regenerated and cooled off, take a hand full of desiccant and put into a glass or metal container. Add enough water to cover the beads. You should get a reaction between the beads and the water – a bubbling action and some heat. If you don’t get this reaction – replace the desiccant.
Poor drying could also be due to the heater elements not producing the proper heat or drawing the proper amperage. Another cause could be air leaks or obstructions in the air hoses
Jeff Rodway, Technical Service Manager, Novatec Inc.
Ask the Expert
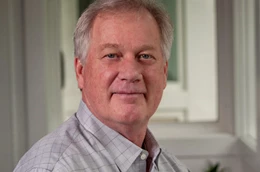