How Different Resin Types Affect Dry Time and Process
Hygroscopic vs. Non-Hygroscopic Resins
What does hygroscopic mean, and how does it affect resin moisture retention and drying?
Hygroscopic Resins
(i.e., Nylon, ABS, Acrylic, Polyurethane, Polycarbonate, PET, PBT,)
- Have a strong affinity to attract moisture
- Will absorb moisture onto their molecular structure if exposed to ambient air
- Internal moisture can not be removed with hot air alone
Water vapor surrounding a hygroscopic pellet is absorbed into the pellet. As the vapor pressure within the pellet increases to equal the vapor pressure surrounding the pellet, equilibrium occurs. This is referred to as, moisture equilibrium.
When an environment of hot, dry air surrounds a wet hygroscopic pellet, the vapor pressure surrounding the pellet is lower than the vapor pressure within the pellet. Consequently, the moisture within the pellet begins to migrate toward the area of low vapor pressure outside the pellet. Expose the pellet to the hot, dry atmosphere for a sufficient period and the pellet eventually reaches moisture equilibrium with the surrounding dry conditions. In other words, the pellet becomes dry.
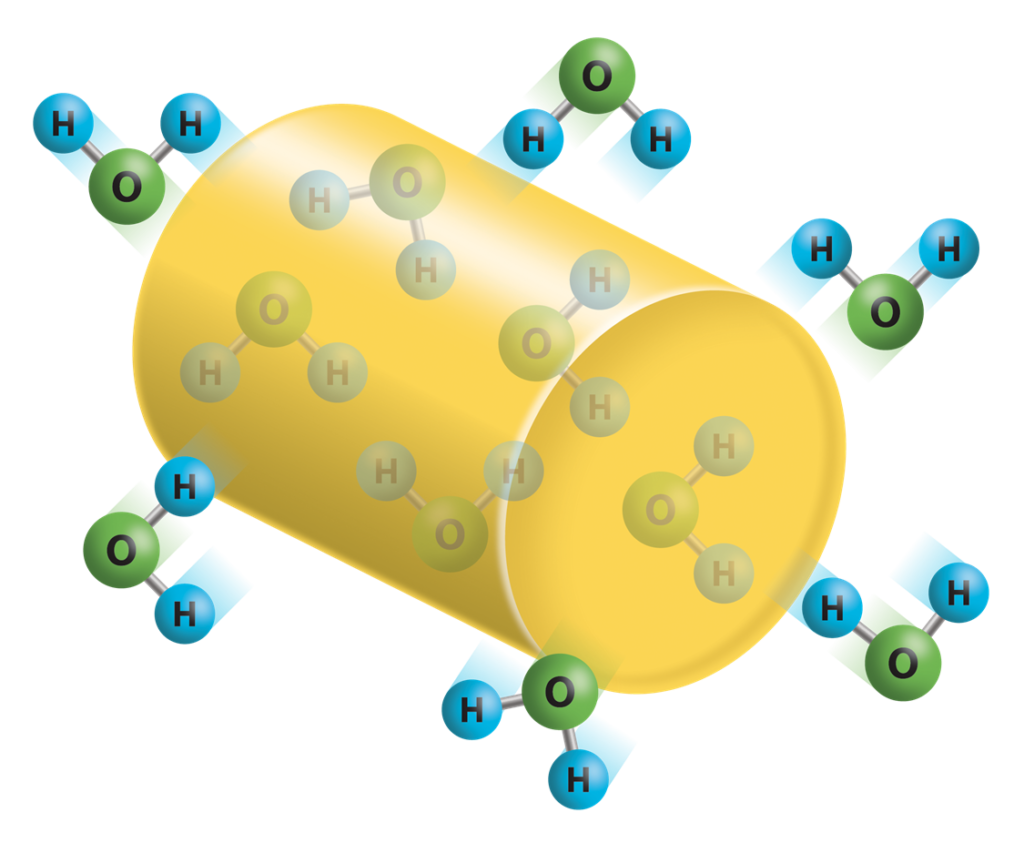
Non-Hygroscopic Resins
(i.e., Polyethylene, Polypropylene, Polystyrene, PVC)
- Do not have an affinity for moisture
- Any moisture collected is adsorbed on the surface of the pellet
- Typical moisture collection is due to condensation
- Moisture is easily removed by passing a sufficient stream of warm air over the material
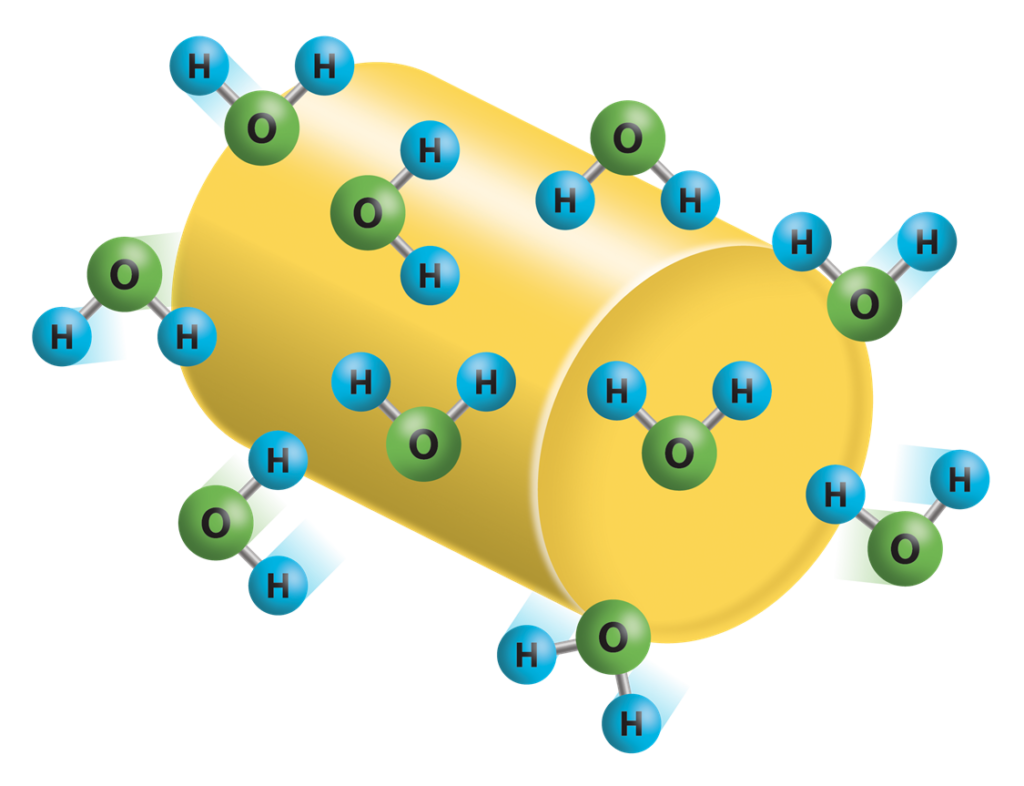
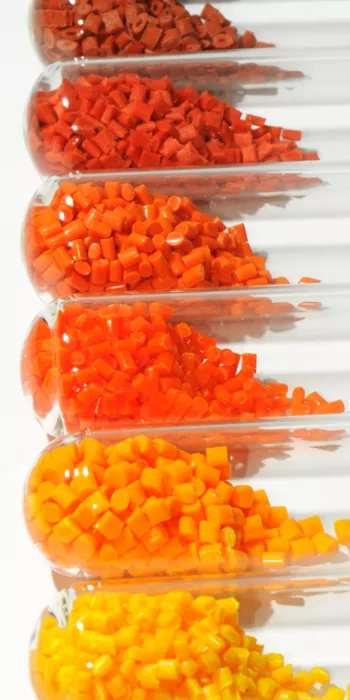
How to Dry Crystalline vs. Amorphous PET for Optimal Processing
All PET (polyethylene terephthalate) materials are hygroscopic, so exposure to a humid environment will cause them to absorb moisture. This moisture causes a cleavage in the polymer chain during melt and results in a degradation of the physical properties of the product produced. In almost all applications, you should dry PET to a moisture content of .005% or less (by weight) prior to processing to ensure molecular weight retention and optimum physical properties.
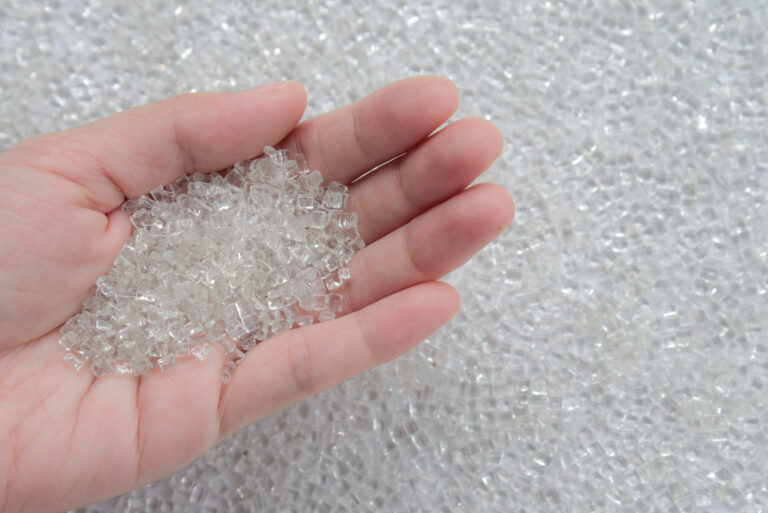
Virgin PET
Virgin PET is usually in a crystalline state (indicated by its white color) when it is purchased from a supplier. It must be dry prior to processing. Using conventional desiccant drying systems, you should dry PET at 300 – 350˚ F. at a dew point of -20 to -40˚ F. for a period of 4 to 6 hours. This reduces the moisture content to .005% or below, ensuring the production of a good product.
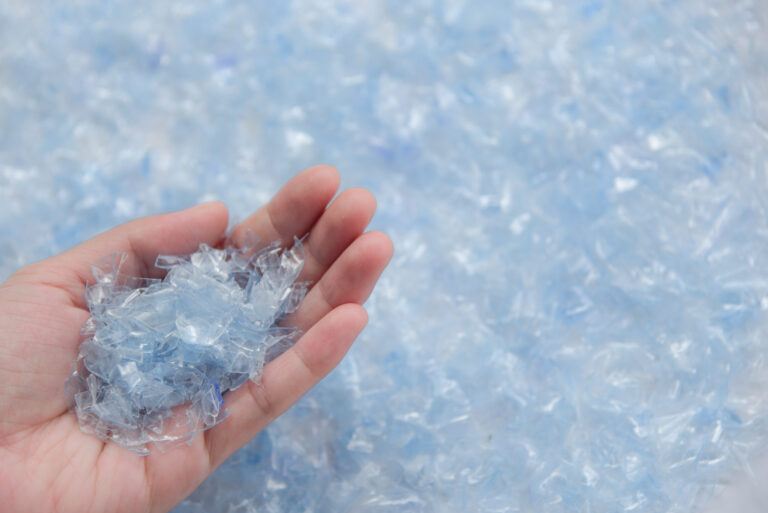
Regrind PET
Regrind PET material is usually not crystalline, but amorphous and clear in color. A characteristic of amorphous materials is that they tend to soften and agglomerate at normal drying temperatures, forming clumps and adhering to the walls of a drying hopper. Crystallize amorphous material, prior to drying, to prevent this agglomeration from occurring. Agitating the material while heating it to a temperature of about 180˚ F for a minimum of 20-30 minutes will convert the material from its amorphous state to a crystallized state, ready for drying. We call this process crystallizing but technically, it is a re-crystallization of the material. Different formulations of PET have different rates of crystallization, ranging up to one hour. Note that if the regrind PET is white in color, it is probably already crystalline and may be dried as-is.There are a couple of methods used for the crystallization/drying process: See PET Desiccant Wheel Energy-Saver Dryer and Infrared Crystallizers/Dryers. Biaxially oriented bottle scrap, regardless of color, is crystalline and should be further crystallized prior to drying – for safety’s sake.
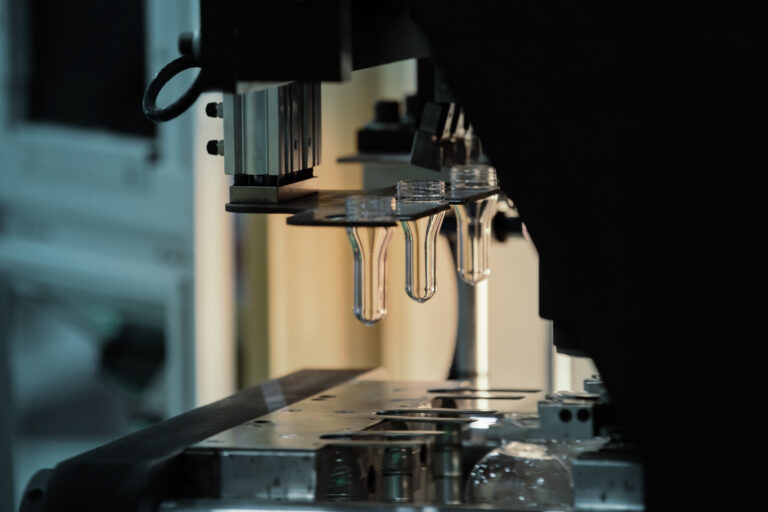
Blow Molded PET
Blow molders, producing scrap often blend the amorphous scrap with crystalline virgin material and dry them together. As a rule of thumb, when the amorphous scrap is less than 20%, and it can be thoroughly blended with 80% or more crystalline virgin material, it can be dried without experiencing agglomeration problems.
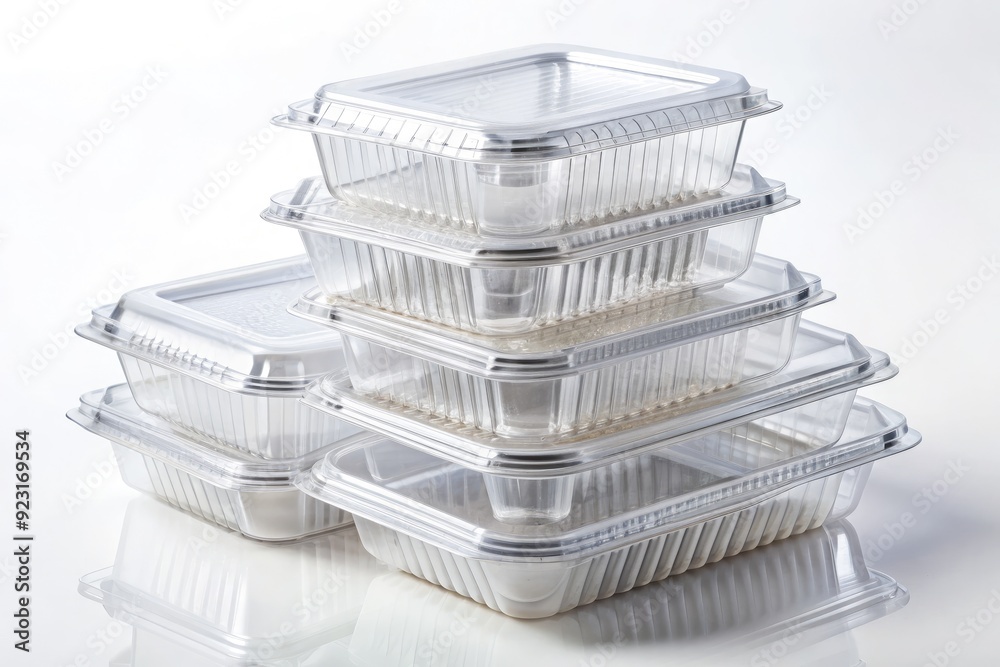
Thermoformed PET
Thermoformers producing more than 20% amorphous scrap and requiring the highest physical properties possible must crystallize the scrap prior to drying to ensure that agglomeration problems do not occur. The minimal web scrap produced by some thermoformers is usually the crystalline white color and it can be dried as-is. If a large percentage of the scrap being produced is clear, it is amorphous and must be crystallized prior to drying.
Drying Blended or Compounded Resin Materials
The blending of materials prior to drying can change the dynamics of your drying task.
Considerations when drying blended resin materials:
- Virgin material, blended with a high percentage of regrind (which is typically much lighter than virgin material), decreases the combined bulk density of the material to be dried. In some cases, this may require a larger drying hopper to provide enough residence time for the drying process.
- Materials mixed by dry blending (not compounded) may separate during the transfer from the blending device to the drying hopper, resulting in uneven drying and worse, uneven or error-filled processing, for example: off-color parts or parts lacking the characteristics to be created by the additive.
- You should not mix or blend materials with very different drying requirements. You should dry those materials separately before blending and processing them.
Considerations when drying compounded resins:
Compounded Resins are quite common in our industry. Sometimes the additive has processing characteristics so similar to the basic resin that you can dry and process in exactly the same manner as is indicated for the main ingredient.
It is essential to consult with your additive supplier to determine their specific drying requirements, such as drying temperature and final moisture content, as well as storage, handling, and processing needs. Making assumptions about drying temperature can result in premature softening in the drying hopper or even gassing that isn’t present in the base resin alone. To ensure optimal performance, it is crucial to communicate with the supplier of any additive regarding all aspects of the new material, from receipt to storage, handling, drying, and processing.

Ask the Expert
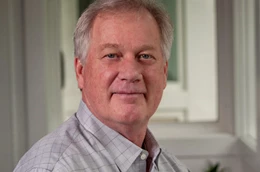